Knowing how to minimize pressure drops requires an understanding of what’s causing them in the first place. There are several factors that can cause a drop in pressure in conveying systems, including overfeeding, insufficient air flow or air velocity, line leaks, and even air moisture. Continue reading to learn what steps you can take to prevent pressure drops caused by these issues.
What Causes Pressure Drops in Pneumatic Conveying?
Before you can figure out how to minimize pressure drops in your pneumatic conveying system, you first need to identify what’s causing the pressure to drop. Usually, it’s a result of one of four causes:
- The pipeline is being overfed, causing the lines to block
- The volumetric air flow rate is insufficient to convey products through the lines
- There is an air leak that’s lowering the air pressure in the pipelines
- There is too much air moisture, causing the material particles to cake and block
Minimize Pressure Drops Caused by Overfeeding
If the pressure drop in your pneumatic system is being caused by overfeeding, the reading on your pressure gauge will be above the design value.
When too much material is being fed into the conveying line, it reduces the amount of pressure available to convey the product through the pipelines. Not only does this cut the conveying capacity of the system, it can also cause the lines to block.
To minimize pressure drops from overfeeding, you must ensure that the conveying lines are being fed at the correct rate. It’s important to monitor and adjust the feed rate because different products have different feed rate requirements.
Similarly, conveying products over different distances will also affect the ideal feed rate:
- The proportions of air required to convey a product correspond to the distance that product is being conveyed over
- If the feed rate isn’t adjusted, the pipeline will be underutilized for shorter distances, and could block over longer distances, resulting in pressure drops
- To prevent this from happening, the product flow rate through the conveying lines must always be the maximum that can be conveyed with the available air flow
To feed material into your pneumatic conveying system correctly and minimize pressure drops, you can do the following:
- Make sure the feed hopper uses a mass flow discharge pattern
- Check your product’s flow properties to determine what design features the feed hopper, as well as other feeding devices need for optimum performance
- Ensure the operating speed of the feeder matches the material’s discharge rate from the feed hopper
- Change the material discharge rate if the feed rate changes
- Vary the rotational speed of the rotor if you need to alter the flow control
- If you need to stop the feed and give the system a chance to clear, install differential pressure switches at all air movers and link them to the product feeder
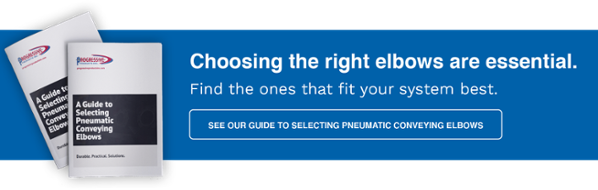
Drop in Pressure Caused by Air Flow Rate
If your pneumatic conveying system has an insufficient volumetric air flow rate, the reading on your pressure gauge will be at or below the design value. When the volume of air flowing in the conveying lines is too low, it won’t be able to convey the product. As in the case of overfeeding, this can lead to blockages and pressure drops.
To ensure the volumetric flow rate and supply pressure needed for your pneumatic conveying system are sufficient, there are a number of air requirements you have to consider:
- You must select the right fan, blower, and compressor
- The air movers must have sufficient output capability
- Different products will require different air flow rates
- Any changes to the air velocity will require corresponding changes to the air flow
Air Velocity
Air velocity is another important factor to consider when trying to minimize pressure drops in your pneumatic conveying system. If this is too low at the product pick-up point, i.e. the start of the conveying line, there won’t be enough force to carry the materials around the conveying system, resulting in blockages and pressure drops.
One way air velocities can become insufficient is if there’s an increase in air supply pressure. This will correspondingly lower the air velocity at the line inlet and potentially cause a pressure drop in the conveying system. It’s important to remember that the air mass flow rate, the volumetric air flow, and the air velocity should all be in proportion to each other.
To avoid pressure drops in your conveying system when the air velocity is too low:
- Maintain the required air velocity by offsetting any increased air supply pressure with additional volume
- Use an air mover with a higher volumetric flow rate to unblock pipelines
- Ensure the air velocity at the line inlet doesn’t exceed the minimum conveying air velocity by more than 20%
Air Leaks
One of the biggest culprits behind pressure drops in pneumatic conveying is an air leak, which lowers the air pressure in pipelines. When line leaks get worse, so does the pressure drop, putting a greater strain on the system to provide enough power and maintain the optimum level of pressure.
In pressure systems, air leaks can occur at pipe joints:
- If compression couplings aren’t tight enough
- If the gaskets are worn
- If there are holes in the pipelines
In vacuum systems, air leaks not only occur at pipe joints for the same reasons, they can also be caused if the airlock is worn.
You should regularly check your conveying system for line leaks in order to minimize pressure drops and keep your system running as efficiently as possible. One way to identify a line leak is if your power consumption has suddenly increased. You should also be able to hear and feel air leakage in your system. If you do, it’s essential to carry out an inspection on the following components:
- Morris couplings
- Tri-clover clamps
- Airlock flanges
- Pressure or vacuum gauge ports
- Blower silencers
- Blower flanges
- Butterfly valves (bypass in blower)
- In-line diverter valves
The Effects of Air Moisture
Moisture inside pipelines can also lead to a drop in pressure in conveying systems. When there is too much moisture in your system’s pipelines, it can cause the material particles to become sticky and adhere to the walls of the conveying lines. If left to accumulate, the material will begin to cake, which can block the flow of gas. This results in a pressure drop.
Moisture usually enters conveying systems when the dew point of the conveying air is higher than the temperature of the material being conveyed. In other words, if the material is colder than the conveying air, water vapour can quickly accumulate on the particle surfaces. On the other hand, if a material enters a cold pipeline, condensation occurs and causes the particles to stick to the pipeline walls.
There are several things you can do to remove moisture from your conveying system and prevent against pressure drops:
- The conveying air can be blown through the pipelines to dry them out before the product is introduced
- Sections of the pipeline that have a build-up of moisture can be exposed to trace heating in order to dry out the air
- To keep the material’s temperature higher than the conveying air’s dew point, you should store the product in a warm room for a few days before conveying it
- If you’re conveying moisture-sensitive or temperature-sensitive materials, like sugar, you should install the necessary equipment to keep moisture away. This could include, for example, air coolers and air dryers
Risks of Pressure Drops in Conveying Systems
From the length and diameter of pipes, to the power of the air mover and volume of bulk material, a drop in pressure in conveying systems can be caused by a number of factors. If proper measures aren’t put in place to mitigate these, it can result in:
- A reduction in your conveying system’s capacity
- Decreased productivity, resulting in money loss
- Damage to pneumatic components as a result of material build-up
- Expensive maintenance and repair work
- Costly periods of unplanned downtime
In addition to everything we’ve mentioned in this article, you should arrange routine inspections of your pneumatic conveying system to ensure its components are running efficiently. This will also be crucial in identifying things like air leaks, which have a number of detrimental effects on pneumatic conveying systems. If your conveying system is suffering from pressure drops, but you’re unsure where the issue lies, always consult an expert before attempting any action yourself. They will provide you with the most effective solutions for your specific circumstances.