Bulk material handling is an essential aspect of various industrial processes, such as manufacturing and mining. The type of machines needed to handle bulk material depends on the type of bulk material itself. Dense bulk materials, like mineral ores, require heavy-duty machines, including metal conveyor belts and minecarts or miner trolleys. Meanwhile, finer and lower density bulk materials, such as flour, can be carried through pneumatic conveying systems.
Bulk Material Handling Explained
Bulk materials include any materials that are dry, granular, powdery, or lumpy in nature, such as cement powder, animal kibble or grains. The way in which bulk materials are handled depends on what the material is. For example, garbage is a type of bulk material with lots of different types of individual constituents, all in different shapes. Therefore, handling it during sorting requires compacting machines.
Bulk material handling is an engineering process of designing machines and structures for moving and processing bulk materials within an area, such as a factory floor. Bulk materials are typically raw materials that need to be processed further. These materials are delivered to the factory or processing facility on trucks, ships or trains. They are then typically unloaded into a large yard or a storage facility using a conveyor belt. In some facilities, pneumatic conveying systems are used, especially if the bulk material is low-density. The materials are then stockpiled in silos.
Some common examples of bulk materials are the following:
- Minerals and ores
- Coal
- Grains
- Sand
- Salt
- Chemicals
- Plastic pellets
- Pet food
- Sugar
- Flour
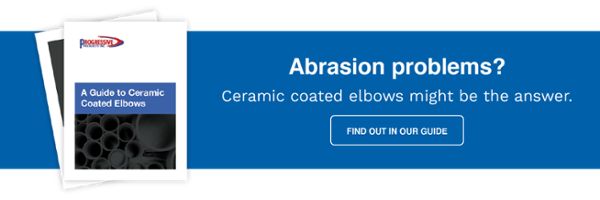
How Does Bulk Material Handling Work?
Bulk material handling is about safely conveying the materials within the factory or processing area. The characteristics of the materials determine the system’s conveying parameters, like the conveyance speed or flow rate. As well as this, the type of bulk material also defines the type of protection the handling system should have. For example, ceramic linings or coatings are sometimes used in systems because some types of bulk materials are abrasive and could damage the system’s components.
Conveying hazardous bulk materials, such as toxic or flammable substances, requires careful handling. For instance, the handling of sulfur powder requires temperature control, meaning that the flow rate should also be carefully calibrated.
Characteristics Of Bulk Materials
Engineers design bulk material handling machines based on the characteristics of the bulk material, such as the following:
- Density of the materials
- Size of particles
- Form (e.g., powder, flake, pellet or granule)
- Liquid content (i.e. moisture content or hygroscopy)
- Material properties such as abrasiveness, flammability, and toxicity
Some bulk materials require special handling to ensure safety. This is particularly true of bulk materials used in food. Food-grade handling of bulk materials requires the equipment and its internal components to be compliant with certain sanitary rules and regulations.
Similarly, conveying requirements for bulk materials used in the pharmaceutical industry include strict hygiene standards, total product containment, and contamination-free operations. Therefore, the type of equipment used to handle bulk materials like wood chips or sand will have different specifications to the equipment used to handle things like cereals or raw materials used in pharmaceuticals.
Important Components Of Bulk Material Handling Systems
The designs of bulk material handling systems vary depending on the industry, factory or processing facility, and the type of material. While many companies require customized designs, there are some standard components.
Fixed structures are permanent components of bulk material handling systems that don’t need to be recalibrated. They include things like:
- Motors
- Conveyor belts or pneumatic conveyors
- Screw conveyors
- Tubular drag conveyors
- Toploaders
- Moving floors
- Stackers
- Reclaimers
- Bucket elevators
- Hoppers
Mobile components transport the materials offsite, deliver them to the processing site, or transport them within the area of the manufacturing plant or processing facility. They include:
- Truck dumpers
- Railcar dumper
- Loaders
- Wagons
- Shiploaders
- Various types of shuttles
Other important components of bulk material handling systems are silos, storage facilities, and stockyards or stockpiles. These are commonly found within the processing or manufacturing site, but usually in separate buildings. More advanced bulk material handling facilities have automated robots and A.I. management systems.
Maintaining A Bulk Material Handling System
Periodic preventive maintenance and repairs are necessary to ensure the efficiency of bulk handling systems. Cleaning, like the removal of rust, should also be carried out regularly in order to optimize the lifespan of the system. Greasing and oiling the various moving parts is also crucial in minimizing friction and improving the longevity of these components.
Calibrating some components for advanced programmable systems is also necessary to ensure safety and efficiency. You should never overload the system or feed materials that can damage it. Controlling the internal climate of a processing or manufacturing plant is also important because things like air stratification and process heat could result in unsafe conditions for the materials, depending on what they are.
Finally, replacing old or damaged components is crucial in bulk material handling systems. Don’t wait until the very last minute to replace something, as this could jeopardize your entire system, lead to downtime, and cost you more money up-front. It’s far more cost-effective and efficient to upgrade or replace old components with high-quality parts - and your equipment will thank you for it in the long run.