To find the correct air velocity in pneumatic conveying systems, it’s crucial to understand the properties of the material being conveyed, such as the size, shape, and density of particles.
These properties also determine how air velocity affects materials, such as high velocities causing soft materials to form angel hair, and low velocities causing heavy materials to block conveying lines.
What is Air Velocity in Pneumatic Conveying?
Air velocity in pneumatic conveying is the speed at which air flows in the pipelines. Sometimes referred to as conveying airspeed, air velocity is required to keep material particles suspended and carry them through the conveying lines.
Without a minimum air velocity, particles will fall out of suspension and cause blockages in the pipelines - this is called saltation velocity.
Air velocity also changes over the length of conveying lines, affected by corresponding changes in pressure and temperature. For example, as pressure decreases along the line, the volumetric flow rate increases along with the conveying air velocity.
This means that air velocity at the product pick-up point is usually always at the minimum value. Since pressure drops in pneumatic conveying systems correlate to the square of the velocity, air velocity must be kept at the minimum acceptable levels to sustain particle suspension throughout the pipeline, as well as to mitigate the risk of pressure drops.
The required air velocity in pneumatic conveying depends on the specific conveying line and the materials it’s transporting. That said, there are some approximations that can be given for different types of systems:
- Dilute phase pressure systems have an end of line air velocity between 20-25 m/s
- Dilute phase vacuum systems have an end of line air velocity between 20-30 m/s
- Dense phase pressure systems have an end of line air velocity between 4-8 m/s
- Dense phase vacuum systems have an end of line air velocity between 5-10 m/s
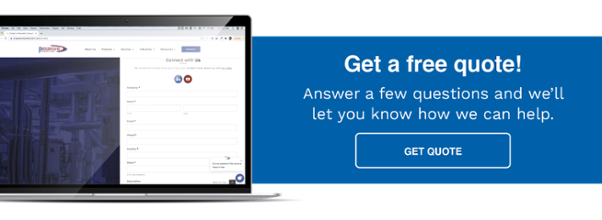
5 Ways Air Velocity Affects Materials
Air velocity in pneumatic conveying directly affects how materials are conveyed. Exactly how air velocity affects materials depends on the size, shape, and density of the particles.
1. Shape
Materials that have particles with larger surface areas, such as cement, require a lower air velocity value than materials like fly ash, which has a more spherical shape. In this case:
- Cement requires an air velocity between 2000-2200 ft/min, or 10-11 m/s
- Fly ash requires an air velocity between 2200-2400 ft/min, or 11-12 m/s
2. Size
How air velocity affects materials with fine, granular particles is reflected in the higher air velocity values required to convey them, which typically range between 2600-3000 ft/min, or 13-15 m/s. But this could fluctuate slightly depending on the width of the particle size distribution.
For example, materials like granular sugar require slightly higher conveying air velocity values of around 16 m/s due to the narrower size of their particle distribution.
3. Weight and density
How air velocity affects materials of different densities and weight is another important consideration. For example, lighter materials could degrade if conveyed through the pipelines at high velocities.
When conveying larger material particles with higher densities, on the other hand, higher air velocities must be used. If the air velocity is too low in these cases, there wouldn’t be enough force to carry the particles through the pipelines, resulting in blockages and pressure loss.
4. Material Dusting and Abrasion
If high air velocities are used to convey hard materials, the material is at risk of shattering, leading to material dusting which can cause a host of problems in your system.
Similarly, if the material is hard and glass-filled, like nylon or polypropylene, high velocities can cause abrasion in the pneumatic conveying system by wearing against the internal components.
5. Angel Hair
Another way in which air velocity in pneumatic conveying affects materials is through the formation of angel hair, also known as streamers. These are detrimental to conveying lines, causing product deterioration, color contamination, clogged filters, and overall inefficiencies.
Caused by frictional heat, angel hair can form when a soft material is conveyed at too high a velocity. This will cause the material to travel quicker through the conveying lines and abrade against the pipe walls. As a result, frictional heat increases, and angel hair is formed.
7 Tips for Getting Air Velocity Right
To get the air velocity right in your pneumatic conveying system, you can use a simple calculation: divide the volumetric flow rate in m3/s by the passing section of the pipe in m2. These calculations must be based on a specific reference position, given the changing nature of air velocity along the length of pipelines.
A few other things you can do to ensure your air velocity is set correctly include:
- Understand your material’s properties and characteristics, including the size, shape, and density of particles
- Determine the solids loading ratio to quantify how much material there is to the air, which will inform the minimum required air velocity
- Add straight pipes between elbows so that materials can get picked up in the air stream and gain velocity as they travel through the pipelines
- Similarly, to ensure that materials reach their terminal velocity as quickly as possible, use the material’s particle size, shape, and density to determine the correct acceleration length of the pipelines
- Recalibrate the air velocity for specific material properties, which can be done by re-sheaving the vacuum pump
- Consider using sensors that monitor airflow and allow you to control the air velocity depending on the material being conveyed
Ensure that the air velocity is kept at the lowest value possible to convey the material so that pressure drops are prevented