Abrasion resistant coatings are crucial to extending the life of your pneumatic conveying system, maximizing production, and saving money. There are several different types of abrasion resistant elbows that can help achieve all of this while covering a range of specific needs. Continue reading to learn how abrasion resistant elbows work, and what their benefits are.
Abrasion Resistant Elbows in Pneumatic Conveying
Abrasion is a common problem in pneumatic conveying systems, as fast-traveling materials come into frequent contact with the interior surfaces of pipes, tubes, line fittings and elbows. When this happens, it causes the components to wear over time.
Pneumatic elbows, especially those located at the end of long runs of pipe, are particularly vulnerable to abrasive wear. This is because more material particles collide with interior surfaces at bends, where they’re forced to change direction at high velocities. As the lifespan of elbows decreases, so does their efficiency, resulting in costly repairs, breakdowns, and periods of downtime. The bottom line? Productivity grinds to a halt.
To safeguard against abrasive wear, abrasion resistant elbows can be used. There are many different types of abrasion resistant elbows in pneumatic conveying, such as Ceram-Back® elbows. These are bare metal elbows that have been encased in a protective ceramic jacket. Once the core elbow has been worn through, the exterior jacket takes on the brunt of abrasion, extending the life expectancy of both the component and the system as a whole.
Other common types of abrasion resistant elbows in pneumatic conveying include:
- Taper Bored Elbows: These feature a thick walled design with taper bored ends, so they fit into the pipe system without creating a ledge. While thick walled elbows won’t prevent abrasion, they’ll dramatically improve the component’s ability to withstand more abrasive wear over time.
- Induction Hardened Elbows: These are sweep elbows made from induction-hardened steel, giving the internal walls a hardness of 600 Brinell in order to maximize their abrasion resistant properties. By comparison, regular steel elbows have a hardness of 125 Brinell.
- Flat-back Elbows, Cement Back Elbows: Flat-back elbows include a flat, steel encasement around the outer curve of the elbow, making them appear square in design. The space between the core elbow and the steel encasement is lined with ceramic tiles in order to improve abrasion resistance. Flat back elbows can be filled with cement instead creating a Cement Back (or Mortar Filled elbow). Both options are suitable for aggregates and larger particle size materials.
- Hollow-back Elbows, Replaceable Back Elbow: A type of sweep elbow that has an empty encasement welded onto the back. This cavity captures the product once it has worn through the elbow, allowing the product to wear against itself, rather than the component. While this isn’t a suitable solution for systems that convey food or materials prone to spoilage or contamination, it’s great for highly abrasive materials that pack well. A Hollowback can have a replaceable back, generally of abrasion resistant steel. A Replaceable elbow has a back that sits on the back of the elbow and does not have as deep of a void as a Hollowback but both capture product and not suitable for food or other spoilage prone materials.
- Porcelain-lined Elbows: The internal surfaces of this type of elbow have been fired with industrial porcelain lining, which lowers the amount of friction wear by allowing materials to slide around, rather than abrade against the surface. The abrasion resistant properties of porcelain lining are also helped by the fact that it has a hardness of 6 Mohs, making it harder than regular steel. That said, they are susceptible to cracking, so shouldn’t be used in the transport of food.
- Tungsten Carbide Clad Elbows: Unlike flat-back or ceramic coated elbows, these bends have an abrasion resistant metal coating on the inside. This is made from tungsten carbide, a dense metal that has a Mohs hardness of 9. In fact, tungsten carbide is one of the hardest metals in the world, being five times harder than tool steel and four times harder than titanium. However, these elbows are only suited for short radii bends because the coating is fairly thin.
- Vortex Elbows: Vortex elbows are mechanised to make the material spin into a vortex, allowing it to move in such a way that the amount of wear caused to the elbow is minimized. This is achieved through a chamber, which is installed on the back of the elbow. Vortex elbows are available in a range of materials and alloys, but they are limited by a range of factors, including line pressure, product flow, size, configurations, and degrees.
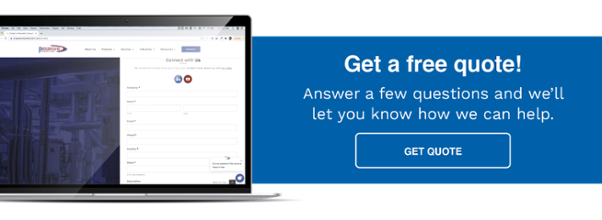
6 Benefits of Abrasion Resistant Elbows in Pneumatic Conveying
1. Reduces Risk of Product Contamination
One benefit of abrasion resistant elbows that you may not have considered is that they can minimize product contamination. For example, when traveling at high speeds, materials like soft plastics can create a lot of frictional heat as they collide with the internal walls of elbows and pipes. This leads to the formation of angel hairs, or streamers, which risk contaminating the rest of the product with different colors.
Some abrasion resistant coatings can help reduce this by minimizing the amount of frictional abrasion. Porcelain lined elbows are particularly suited for this as they allow the material to slide around. Vortex elbows can also reduce the amount of friction but do not reduce risk of of contamination.
2. Protects Against Corrosion and Oxidation
Abrasive wear isn’t the only killer of pneumatic elbows; corrosion and oxidation are just as detrimental. Metal alloys, like steel, readily oxidize when exposed to oxygen, which can happen when materials abrade against the inner surface of components, leaving scratches. These scratches kickstart oxidation, resulting in rust, degradation, and the need for a replacement part.
Using abrasion resistant elbows in pneumatic conveying systems will protect the component from corrosion and oxidation. For example, abrasion resistant ceramic coatings or cement-filled hollow-back elbows act as a bulwark against further damage once the core elbow has been thoroughly corroded or oxidized.
3. Protects Against Chemical Attacks
Abrasion resistant elbows are also an excellent precautionary measure against chemical attacks, which occur when corrosive substances like acids or soaps come into contact with metal components. This can severely corrode the elbow and weaken it to the point where a replacement is needed - which can be expensive and time-consuming.
However, by coating a metal elbow with a ceramic lining, for example, the impact of chemical attacks will be transferred away from the metal component. As the ceramic coating is much more capable of withstanding chemical attacks, it can massively extend the life expectancy of the part.
4. Extends Lifespan of the Component
Extending the lifespan of pneumatic elbows is another huge benefit to using abrasion resistant coatings. When critical components, like elbows, are protected against abrasive wear, corrosion, and chemical attacks, they can operate at higher efficiency levels and for much longer.
This not only extends the life of the component itself, but also the service life of the entire system as it will be less prone to knock-on maintenance issues and expensive breakdowns.
5. Increases Productivity
A better service life equals higher productivity. When bare pneumatic elbows become worn or corroded as a result of material abrasion, it can lead to costly repairs and periods of downtime. This halts production and, consequently, loses a lot of money.
Because abrasion resistant elbows can last for much longer than bare elbows and because they help optimize the entire pneumatic conveying system, they mitigate the risks of maintenance repairs, replacement parts, and plant shutdowns. This keeps production running at full steam.
6. Saves Money in the Long Run
When fewer repairs and replacement parts are needed and when downtime is minimized and productivity maximized, the result is a ton of money savings. While abrasion resistant elbows might initially be more expensive than the cost of bare elbows, the money you’ll save in the long run more than makes up for it.
Selecting the right elbow for your pneumatic conveying system can be challenging.
At Progressive Products Inc., we supply a range of pneumatic elbows, from hollow-back and replaceable back elbows to the patented Ceram-Back® elbow. If you need help finding the solution that’s right for your specific needs, contact us today.