The differences between pneumatic conveying vs. mechanical conveying come down to the types of bulk materials these two types of systems transfer, the distances they can convey over, and how they are designed.
Put simply, pneumatic conveying is an enclosed, flexible system that uses a gas stream to move dry bulk materials that have a tendency to fluidize. Meanwhile, mechanical conveying is an open system optimized for transferring heavier materials, or those with a high moisture content.
A Brief Overview of Pneumatic Conveying
Pneumatic conveying is the process of transferring dry bulk materials through an enclosed pipeline using a suspended gas stream, which is usually air or an inert gas.
In these systems, materials are discharged from a feed hopper, and feeders are used to control the rate of material flow. Air velocity at the product pick-up point then carries the material particles through the pipelines.
To get the material to the end of the system, a pressure difference between the start and end of the pipeline is required. This necessitates the use of conveying blowers or compressors. Other vital components in pneumatic conveying systems include:
- Material introduction point
- Material feed device (feed hoppers and feeders)
- Air source
- Conveying line
- Air-material separator
- Pneumatic conveying elbows
- Pipelines
- Gaskets
- Airflow movement device
- Receiving point
Material intake points in pneumatic conveying systems use upstream positive pressure blowers to move bulk materials. At the end of the line, the particles are isolated from the air using filter receivers or cyclone separators.
Because of their design, pneumatic conveying systems are best suited for transferring fine or granular bulk materials that are either free-flowing or semi-free flowing. Materials include cement, powders, sugar, salt, plastic pellets, grain, and so on.
There are a few different types of pneumatic conveying systems. The most common are:
- Positive pressure systems: The simplest design, these use blowers or fans to suspend material particles in an airstream
- Vacuum systems: These use a vacuum at the end of the conveying line to pull rather than push materials through the pipelines
- Dilute phase systems: Convey lighter materials, like talcum powder, at fast velocities and high pressures, using a blower to suspend them in an airstream
Dense phase systems: Convey heavier, more abrasive materials, like plastic pellets. Unlike in dilute phase, dense phase can’t suspend these materials, and so uses high air velocity so that the product can travel in waves, meaning less abrasion
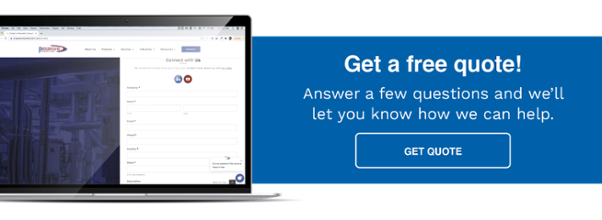
What is Mechanical Conveying?
Mechanical conveying is the process of transporting usually heavy bulk materials using traditional machinery. Hundreds of moving parts are used in mechanical conveying systems. Some of the most important ones are:
- Belts
- Buckets
- Chains
- Driver motors
- Rollers or sprockets
The motor supplies energy to the conveyor, allowing the materials to be conveyed quickly. Usually, mechanical conveying systems are open, such as production lines in a factory, though they can be closed if transferring air-sensitive materials.
Mechanical conveying is best suited for heavy, non-free-flowing materials, like crushed rock or gravel. It’s also the preferred system for materials with a high moisture, fat, or oil content, like cake mix, titanium dioxide, and brown sugar.
There are many different types of mechanical conveying systems, but the most common include:
- Screw conveyors: Commonly transport wet materials horizontally using an auger-type motion. Optimized for small areas and distances less than 24 feet
- Drag chain conveyors: Materials are transported using a chain and paddle design. En masse drag chain conveyors are best for moving dry products over long distances. Bulk flow drags are best for moving wet products at steep inclines
- Bucket elevators: As the name suggests, these are used when products need to be elevated to high positions
- Vibrating feeders: These use vibrating trays that are ideal for the transportation of moist products that are at risk of clumping or sticking
- Belt conveyors: Ideal for moving a lot of materials over very long distances because of the use of a wide belt on top of rollers, which provides a fast yet gentle transport
5 Differences Between Pneumatic Conveying vs. Mechanical Conveying
The most obvious difference between pneumatic conveying vs. mechanical conveying is how they’re designed. While pneumatic systems either use a gas stream or a vacuum, mechanical systems transfer products using machinery, like belts, rollers, and motors.
Another key difference in their design is that pneumatic conveying systems are fully enclosed, while mechanical conveying systems are usually open. But there are many more differences besides design:
- Types of material
Perhaps the most important difference between pneumatic conveying vs. mechanical conveying are the types of materials they’re optimized to transport.
We mentioned them briefly earlier, but in general, pneumatic conveying is best for free-flowing, granulated dry materials, like cement, flour, kibble, or pellets, while mechanical conveying is best for heavy, friable, or wet materials.
Pneumatic conveying systems aerate fine, dry powders, allowing them to be carried efficiently through the pipelines. These materials would be more difficult to convey mechanically due to their tendency to fluidize, which could lead to material loss and the clogging of mechanical parts.
Similarly, wet products are more successfully transported via mechanical conveying because in pneumatic systems, they can quickly cake and cause blockages in the pipelines.
Due to the enclosed system, pneumatic conveying is also better for transporting hazardous materials because it reduces the risk of spillage, and the presence of inert gas can prevent explosions. Mechanical conveying, on the other hand, is better for transporting temperature- or air-sensitive products, which may be compromised in pneumatic systems given the large volumes of flowing air.
- Industries they’re used in
Given the different types of materials, each conveying system has its own group of industries it’s commonly used in. Pneumatic conveying, for example, is the preferred method in food and beverage, pharmaceutical, and plastic and polymer industries.
The robust nature of mechanical conveying makes this method ideal for high-intensity sectors, including mining, agricultural, packaging, manufacturing, and automotive industries, where large quantities of heavy products need to be conveyed very quickly.
- Conveying distance
Another difference between pneumatic conveying vs. mechanical conveying is that the former is best suited for long distances, while the latter is ideal for shorter distances.
This is because with pneumatic conveying, the same amount of equipment is needed no matter what the distance is, making it less efficient and more expensive to use short conveying pipes or tubes. Additionally, while both conveying systems can be used for long distances, it’s often cheaper to install a conveying pipeline than it is to install a mechanical structure.
Longer conveying distances also involve multiple direction changes. With mechanical conveying, this would require the installation of several conveyors because of the limitations of the parts. But with pneumatic conveying, the system is flexible enough to accommodate long and tight bends by using elbows.
- Material routing
Aside from conveying distance and directional changes, there are also differences between how pneumatic and mechanical conveying systems are able to route materials horizontally and vertically.
Pneumatic conveyors can’t be routed at any angle other than straight horizontal or straight vertical. This is because the system doesn’t perform well when there’s a change in gravity, and conveying at an angle could create more friction, leading to wear and abrasion.
Meanwhile, mechanical conveyors are unable to make tight bends. If a turn is needed in a mechanical conveyor, it needs to have a larger bend radius. Pneumatic conveyors, on the other hand, can achieve very tight bends in their pipelines.
- Installation
Its flexibility in material routing makes a pneumatic conveying system relatively easy to install in a given facility. The ability to route the pipelines around existing equipment or obstructions, and accomplish tight bends, also creates more floor space.
The comparably inflexible design of mechanical conveying lines means that these systems often minimize floor space, requiring existing machinery to be relocated, which is a both time-consuming and costly process.
Another difference is that pneumatic conveying systems can be installed both indoors and outdoors given the enclosed nature of the system.
Pros and Cons of Pneumatic vs. Mechanical Conveying
All these differences between pneumatic conveying vs. mechanical conveying highlight pros and cons for each system.
Pros for pneumatic conveying:
- Material routing is simplified and much more flexible than in mechanical systems
- The enclosed line minimizes material loss and potential spillages
- Conveying lines are easily adapted to a facility’s dimensions, taking up less room
- Less maintenance is required because there are fewer moving parts
- This means the system can operate at higher productivity and efficiency levels
- Pneumatic conveyors are safer because components are sealed in enclosed lines
- Air-sensitive products, like sugar, are protected and kept dry within the pipelines
- Abrasion can be easily minimized with wear-resistant components
Cons for pneumatic conveying:
- Expensive to convey over short distances
- Lines can only be horizontal or vertical
- Can’t convey wet products that tend to cake
- Requires more power and energy to operate
- Submicron powders can clog filters
Pros for mechanical conveying:
- Are more cost effective when conveying over short distances
- Lines can be positioned at any angle, some systems can even achieve right-angles
- Heavy products are more easily conveyed because of traditional belt lines
- Lines with slower speeds can transport friable materials without causing damage
- Materials with high moisture, oil, or fat content can be moved without clogging
- Submicron powders can be safely conveyed in flexible screw systems
- Mechanical conveyors cope better with large production rates
- Systems require 10 times less horsepower, making them more energy efficient
- Cheaper design and installation than for pneumatic conveying systems
Cons for mechanical conveying:
- Less safe because of the amount of exposed moving components
- Mechanical parts wear faster, requiring constant maintenance and repairs
- This results in more periods of downtime and increased running costs
- Require a lot of floor space when being installed
- Aren’t able to accommodate tight bends or angles
- Conveying over long distances can be inefficient and costly
Both pneumatic conveying and mechanical conveying have their advantages and drawbacks, depending on the processes they’re intended for. The bottom line is that both systems provide efficient transportation for the materials they’re designed to handle, and choosing which one to go for will entirely depend on your specific needs.